http://www.armortek.co.uk/TaperlockLR.jpg
.......do not seem to coincide with the taper lock that I have.
According to those instructions, there are 2 threaded holes in the taper lock, but on mine, there is only one.
Naff looking arrow, shows the only threaded part.
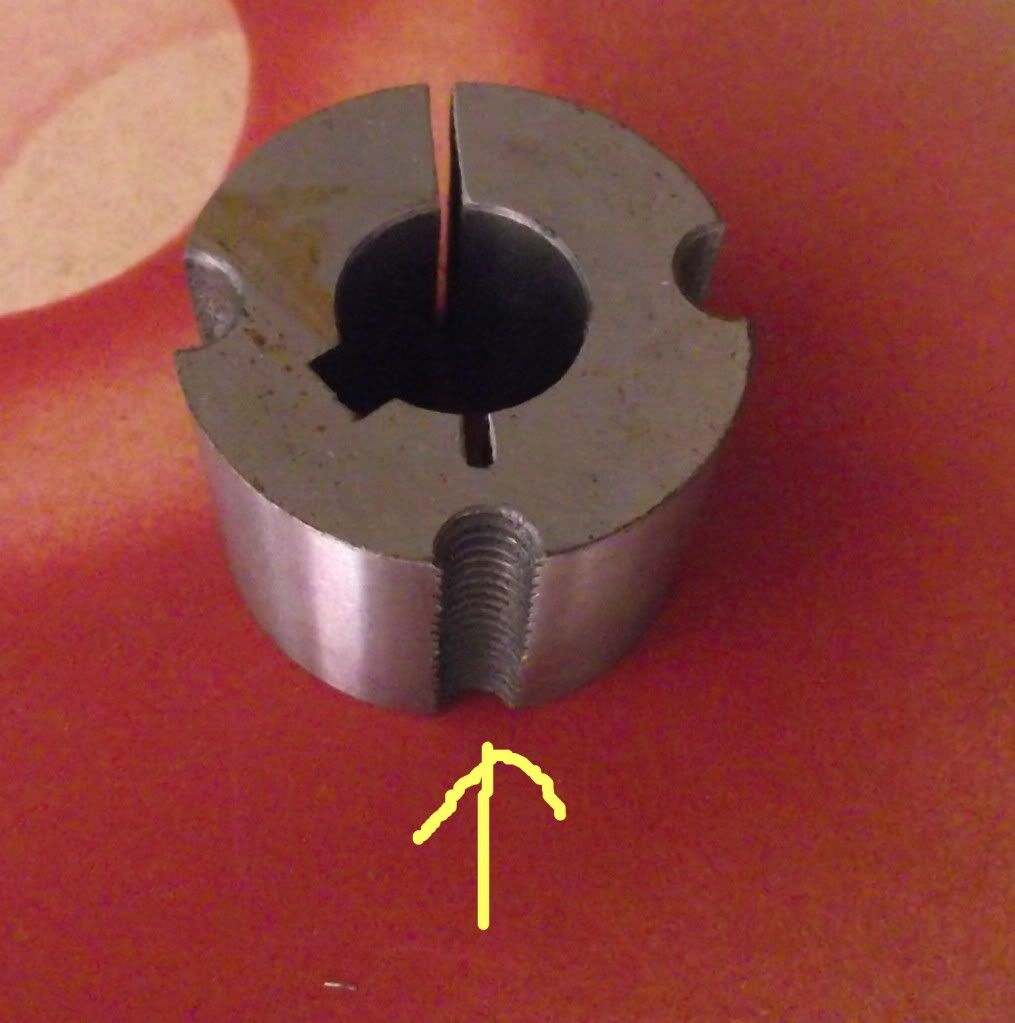
Although my sprockets have two threads.
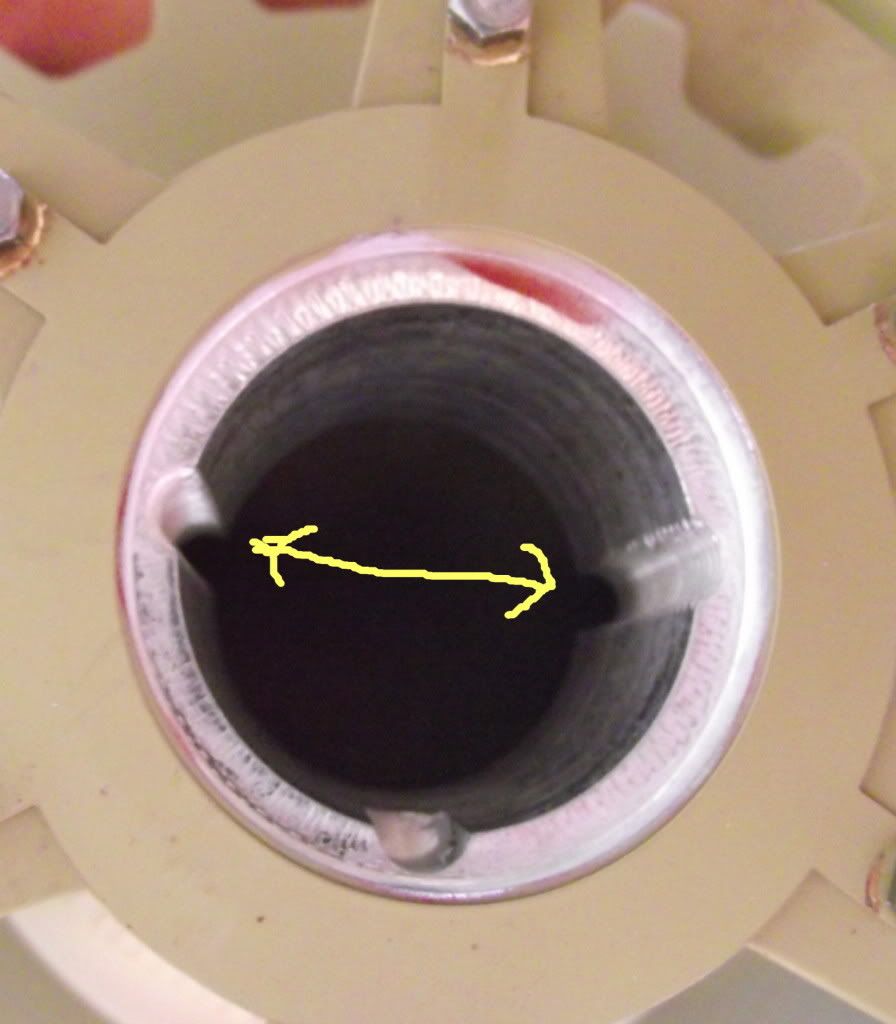
Threaded hole lined up in sprocket.
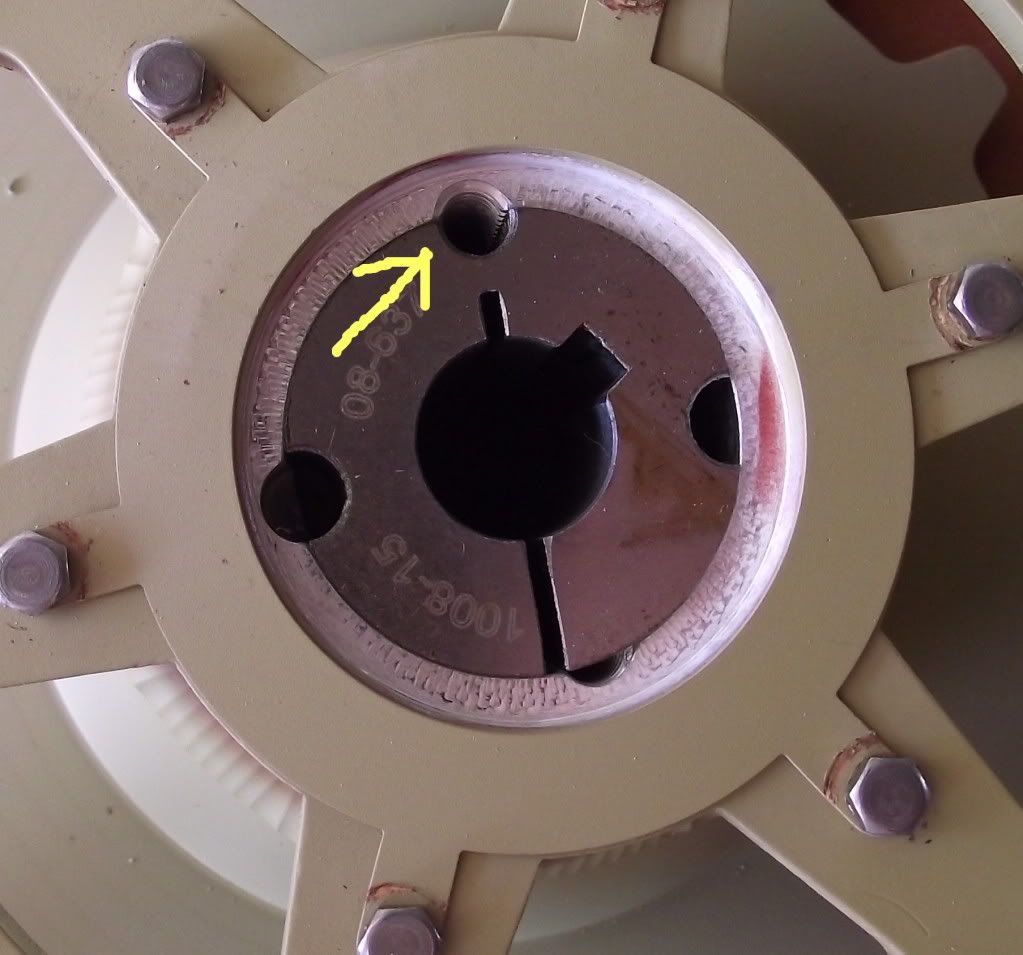
Has something been changed, and the instructions not updated, or have I read the instructions wrongly?
Ta muchly.