Hi All,
Update 18 Aug 20
It is about a year since I got the kit from Stephen and I am still not ready to assemble the basic hull

! Whilst waiting for some fasteners to help with the engine deck I decided to make a start on the road wheels.
The late pattern Tiger 1 resilient road wheels were constructed partly from two circular plates that were held together with M20 bolts. These bolts had a 30mm A/F nut and so the standard M2.5 nut at 5mm A/F is just right. The inner hub consisted of three tapered sections that bolted through to another set on the other side. One set had a tongue that locked into a groove on the axle. The bolts securing these were M14 on the King Tiger and started as M10 on the Tiger, upgraded to M12 later. Knupfer Modell-und Feinwerktechnik market M2.5 bolts and nuts which are 3.5mm A/F which is 21mm A/F at 1/6 scale this is close enough, for me, to the scale 19mm A/F used with a M12 bolt.
After much consideration and design work in Fusion 360 I have decided to stick with the kit supplied solid rendition of the resilient wheels. The main reason being that the new versions are thinner at the hub and this would have involved replacing the spacing tube for the more widely separated (outer) sets of wheels. Simply using spacers to make up the difference was not viable as this would change the position of the bearings relative to the hull sides and result in a requirement to replace the axles.
The different hub bolt arrangement on F01 when compared to that in the kit has been resolved by custom 3D printed nylon hubs. I reckoned that all 15 M2.5 bolts were not required for strength purposes, especially considering that the Early Tiger 1 kit only used 6, and that I could just use the 9 that matched up replacing the other six with heads glued into the hubs. The hole for these ‘faux’ bolts were made deliberately undersize so that a positive ‘push/screw’ fit could be achieved.
Front view of original hubs – Armortek Stock Configuration.
Front view with revised (3D printed) hubs with standard M2.5 nuts. Note etch primer on wheels.
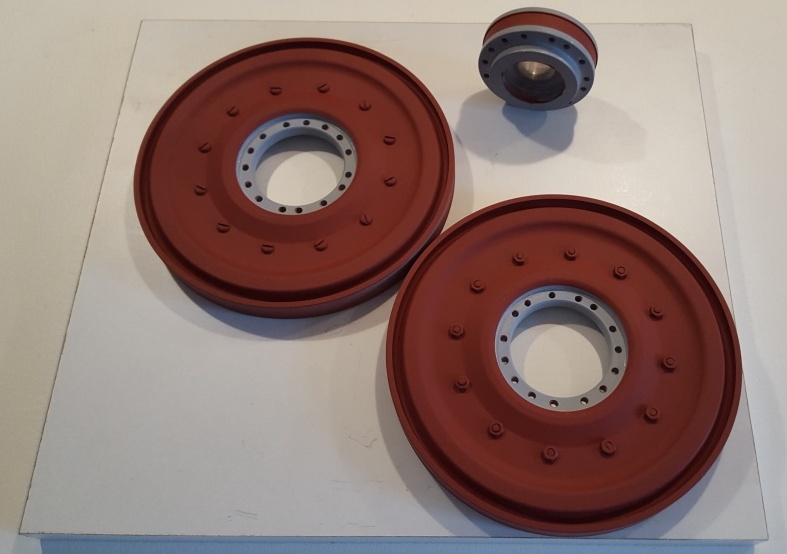
- 20200814_135600-doc.jpg (102.3 KiB) Viewed 4310 times
Inner set with inner faces primed using basic Halford’s Red Primer. Will be assembling this unit prior to spaying base colour (Dunklegelb) as I assume this mimics the production process. Not too worried about true colour match here to RAL 3009 as it will be hidden. In fact, I plan to use this primer for all surfaces that will be oversprayed with the base colour.
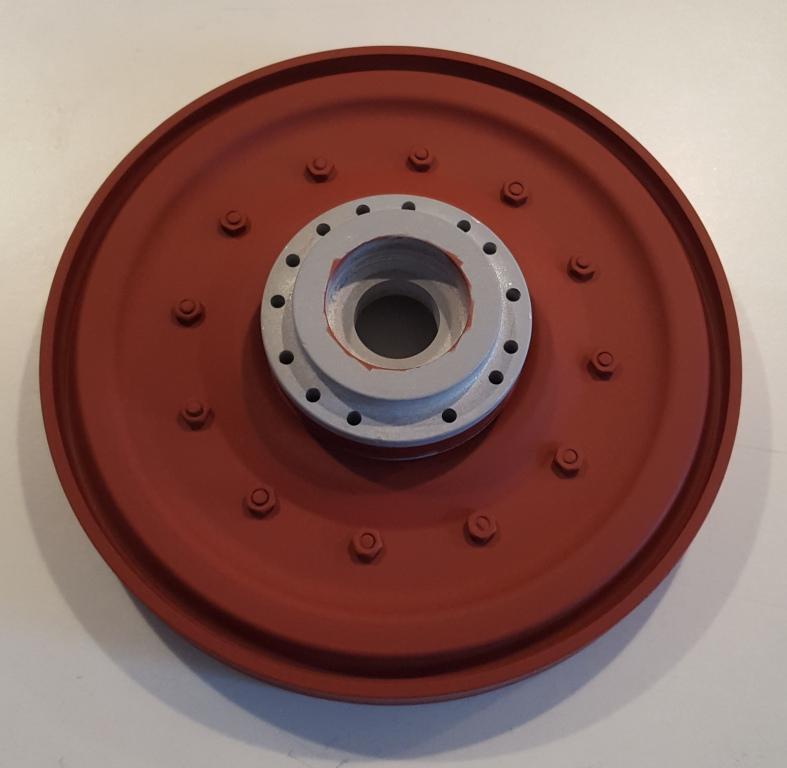
- 20200814_135636-doc.jpg (46.57 KiB) Viewed 4310 times
Spacer in place. I will probably use adhesive to help secure wheels to hubs as well as the bearings.
Rear face of inner wheel set. I have added hex bolts in the holes to mimic those required for securing the actual wheel plates together. I have also added a hub for improved detailing and to shield the bearing from debris etc.
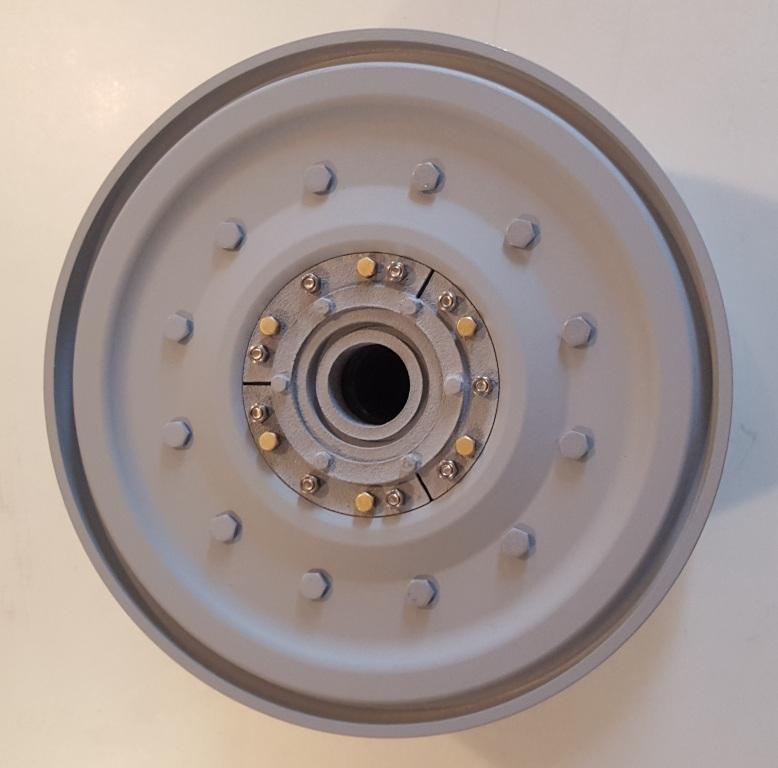
- 20200814_165614-doc.jpg (49.77 KiB) Viewed 4310 times
Rear face of outer wheel set, again note hub.
Front face of outer wheel set. Note the 3d printed replacement hub. I have not added the faux bolt heads yet as I want to check the utility of the printed internal thread for the hubcap. The smaller nuts really disguise the fact that the bolts are the same diameter.
Outer wheel set showing nut retention plates and standard bolt head size used on the spacer (You will not see these) so I get the benefit of a greater surface area for the fastener. I will probably still use some adhesive here.
Front view of both sets (checking clearance of bolts etc.).
Rear view of both sets. Design update: thread for hub cap was too fine to work in this material so have increased it to M20 x 2.5. May need to increase fit tolerance too, we shall see.
Alastair