Page 1 of 1
PTFE as a bearing surface
Posted: Tue Jan 19, 2010 11:12 am
by Adrian Harris
Seeing Derek using PTFE to make a washer for his Stug gun traverse made me wonder if anyone has tried using it in the drive train.
I was thinking of using it to bulk out the gear casing on the prototype Sherman, as there is very little clearance between the sprocket and the gear casing and a noticeable amount of "slop" in the gear system.
I know PTFE is very slippery, so I wouldn't expect it affect the drive performance but how hard wearing is it in this type of application
I'm worried the gears may just carve it away and turn it into PTFE shavings
Adrian.
Posted: Tue Jan 19, 2010 10:28 pm
by Allan Richards
Adrian,
PTFE is a low friction material that is good for bearings. Bearings made from it can also be lubricated with water. If I understand right you want to move the sprockets out a little on the Sherman for the tooth ring bolts to clear the gear housing, but in that application a brass washer would probably be best. Did the prototype Sherman have the taper lock bushes to hold the sprockets? You also mention the slack in the gear train, it won't be easy but you want to check the clearance between the teeth, if it is excessive then you need to rectify this to prevent wear or in extreme cases jumping of the gears. A good mesh is when some paper will just go through the gears without being mashed up.
Posted: Wed Jan 20, 2010 8:43 am
by David Pengelly
I have had experiance with ptfe as a bearing surface on a few occasions . Each time i have been suprised by the results
if its possible to get 2 ptfe washers together then that surface will be like " ice on ice ".
Posted: Wed Jan 20, 2010 10:07 am
by Adrian Harris
Allan,
The prototype is unusual in that it pre-dates the use of taper-locks. The sprocket end cap bolts to both the end of the drive gear shaft and the sprocket centre.
The only way to move the sprocket out further would be to pack out the bolt between the cap and the gear. This might be possible but until I get all the bogies etc back on I don't know how much leeway I have with track alignment.
The "slop" I was referring to is the back and forth play of the main drive gear. I was planning on putting a large "washer" between the large drive gear and the drive casing, (gently) forcing the drive gear outwards to maximise the clearance. Mulling it over last night, I could also put a washer between the sprocket centre and the gear casing, which would prevent wear there and provide a little further packing.
I've ordered a 1mm sheet of PTFE from eBay, though given David's suggestion of using it back-to-back, I will also get the 0.5mm and 0.25mm thicknesses and try combinations together.
Adrian.
Posted: Sat Jan 23, 2010 5:29 pm
by Robert E Morey
Adrian,
I've used PTFE as a washer. It works ok, but is very soft and will be galled easily (but still function ok). Also thin PTFE will distort under pressure. It will probably work well as a washer behind the drive gear if you can hold it in place somehow. I use oil impregnated bronze or brass for all bearing washers etc. Another idea is the spacer you mention. Here is the sprocket spacer I used on the Panther and Sherman. It helps keep the sprocket the exact stand off distance required to the gear case. It should also help prevent the sprocket from grinding into the gear case. The Taperlock just slides up to this bushing -makes removing and reinstalling the sprocket easy and repeatable. The concept will also work without Taperlock bushings, just machine the bushing to touch the rear of the sprocket. As long as the sprocket is secured to the hub cap with M5 screw in center of drive gear spindle, the drive gear should not move side to side.
This bushing is made of brass, since it is not a bearing, it can be made from alum, steel, brass, plastic etc. So far it has worked well as keeping the sprocket spaced away from the gear case.
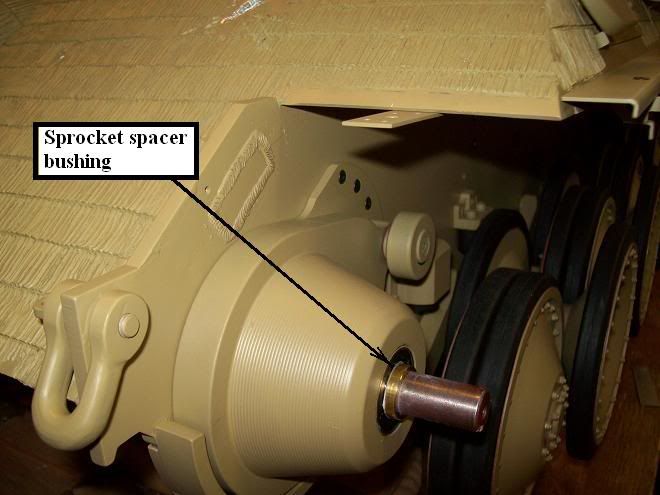