Steve,s Panther build
-
- Posts: 101
- Joined: Wed Jan 21, 2009 5:20 pm
- Location: Parma - Italy
-
- Posts: 142
- Joined: Fri Jan 11, 2008 7:36 pm
- Location: Genoa
- Been liked: 1 time
- Contact:
-
- Posts: 425
- Joined: Sat Dec 04, 2010 11:18 am
- Location: Northern Sweden
- Has liked: 6 times
- Been liked: 194 times
Thanks Steve, much appreciated.Steve Norris wrote: Kent,
There is a 4mm gap between the swing arm and hull side
4mm that will do so now another one to the "must have list"...
Another question now when I look at the photo I posted above.
This new release Panther kit does it have the hull bottom plate divided with a thicker one at the front? (as I believe the KT kit had looking at builders photos).
I have been told it is now made of aluminium and that sounds good.
Reason for asking is that I am putting up a list of upgrading parts for my own build to order from Gill.
Thanks in advance.
Kind regards
Kent
It´s all in the details!
-
- Posts: 1228
- Joined: Thu Jul 12, 2007 11:42 am
- Location: Manchester
- Has liked: 8 times
- Been liked: 697 times
Hi Kent.
After a trail fit of the Anschlagbock i have come to the conclusion that the set up i have does not give enough clearance between the bolt heads and swing arm, the bolt heads protrude almost 1mm and just touch the swing arm. After a rethink i am going to drill all the bolt positions 11/32" through the plate to simulate the counterbores then attach the plate to the hull side using 3x M3 csk bolts which will be filled so that they will not be visable. The bolts will then be fitted into the drilled holes.
I will post some photos soon to show what i have done.
The Hull bottom plate is indeed ally, but just 1 piece without any step.
Regards
Steve
After a trail fit of the Anschlagbock i have come to the conclusion that the set up i have does not give enough clearance between the bolt heads and swing arm, the bolt heads protrude almost 1mm and just touch the swing arm. After a rethink i am going to drill all the bolt positions 11/32" through the plate to simulate the counterbores then attach the plate to the hull side using 3x M3 csk bolts which will be filled so that they will not be visable. The bolts will then be fitted into the drilled holes.
I will post some photos soon to show what i have done.
The Hull bottom plate is indeed ally, but just 1 piece without any step.
Regards
Steve
-
- Posts: 425
- Joined: Sat Dec 04, 2010 11:18 am
- Location: Northern Sweden
- Has liked: 6 times
- Been liked: 194 times
Thanks!Steve Norris wrote:The Hull bottom plate is indeed ally, but just 1 piece without any step.
Ok, no problem I have to go for plan B instead.
I think I got the picture and believe the csk bolts will be the way to go.
Has a good photo of the Houffalize Panther from Sven Strobbe that I think he wants for everyone to see.
Might give a hint how this one looked, please note how the bolt heads are "sunken" into the holes.

The "tube" left/high has nothing to do with a real Panther it’s just to get wheels on this display relic.
Kind regards
Kent
It´s all in the details!
-
- Posts: 1228
- Joined: Thu Jul 12, 2007 11:42 am
- Location: Manchester
- Has liked: 8 times
- Been liked: 697 times
A little update on the Ansclagbock.
The first shot shows the dummy attachment bolts in position, 2 more bolts fit forward of these but because of the position of one of the torsion bar block attachment screws it was not possible to drill and tap at that position. Also shown are 3 predrilled and tapped holes for attaching the Anschlagbock plate.
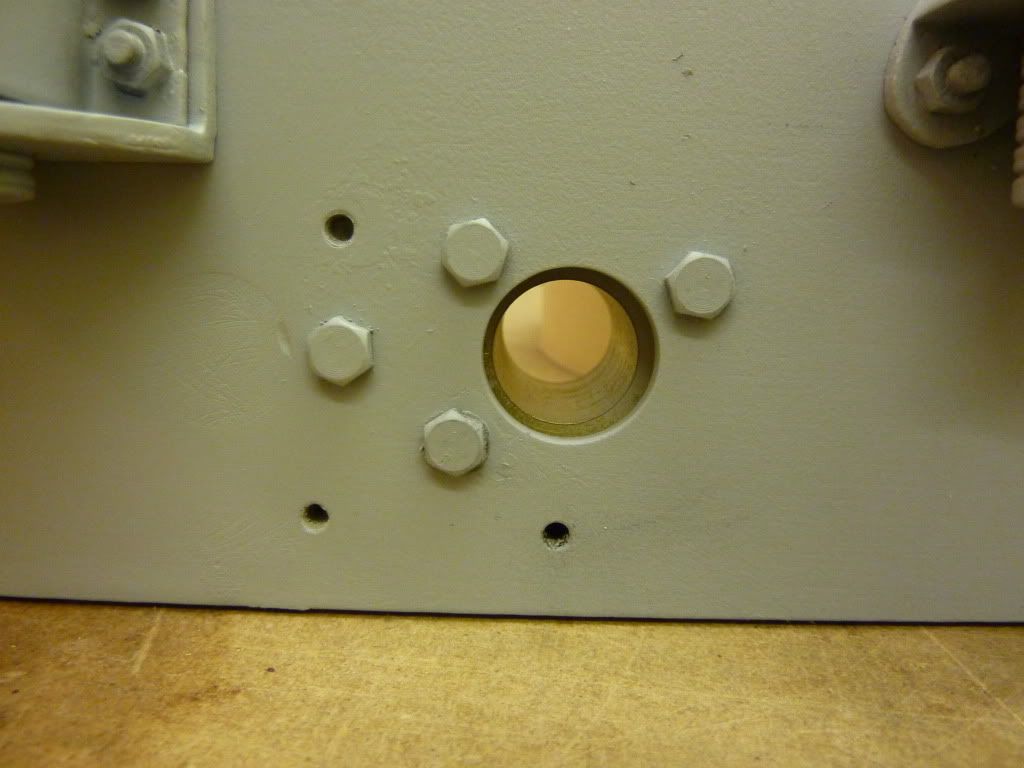
The next shot shows the Anschlagbock plate installed using 3 M3 csk bolts.
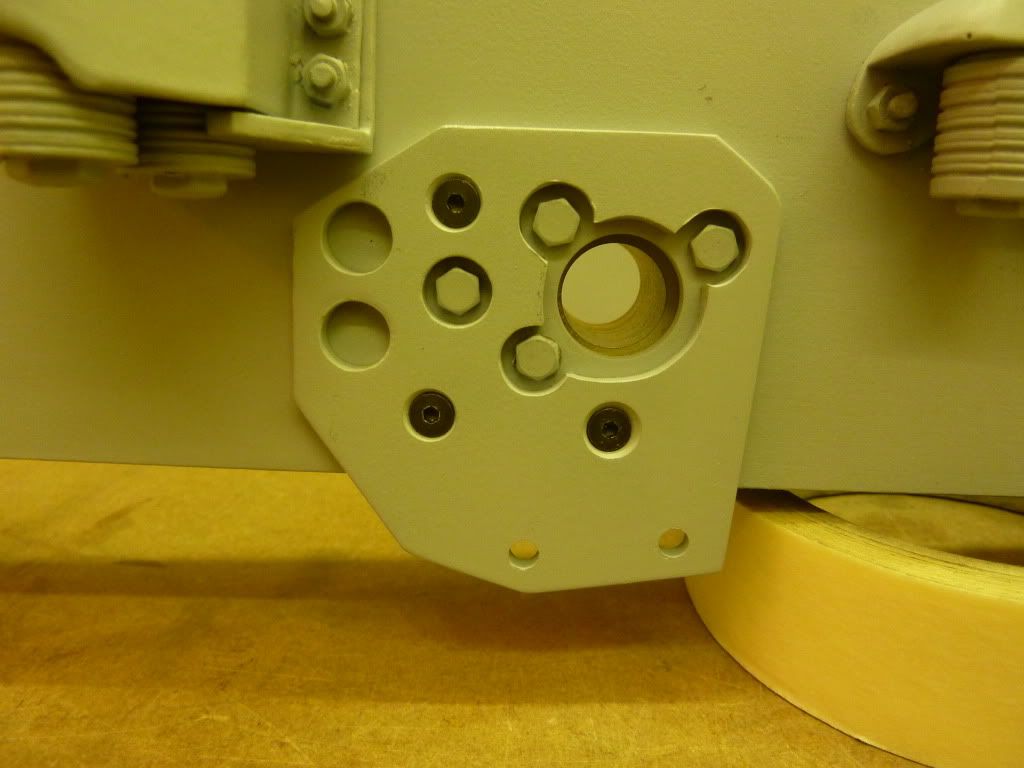
The next shot shows the final appearance of the Ansclagbock with the mounting screws filled and the 2 dummy bolts glued in place
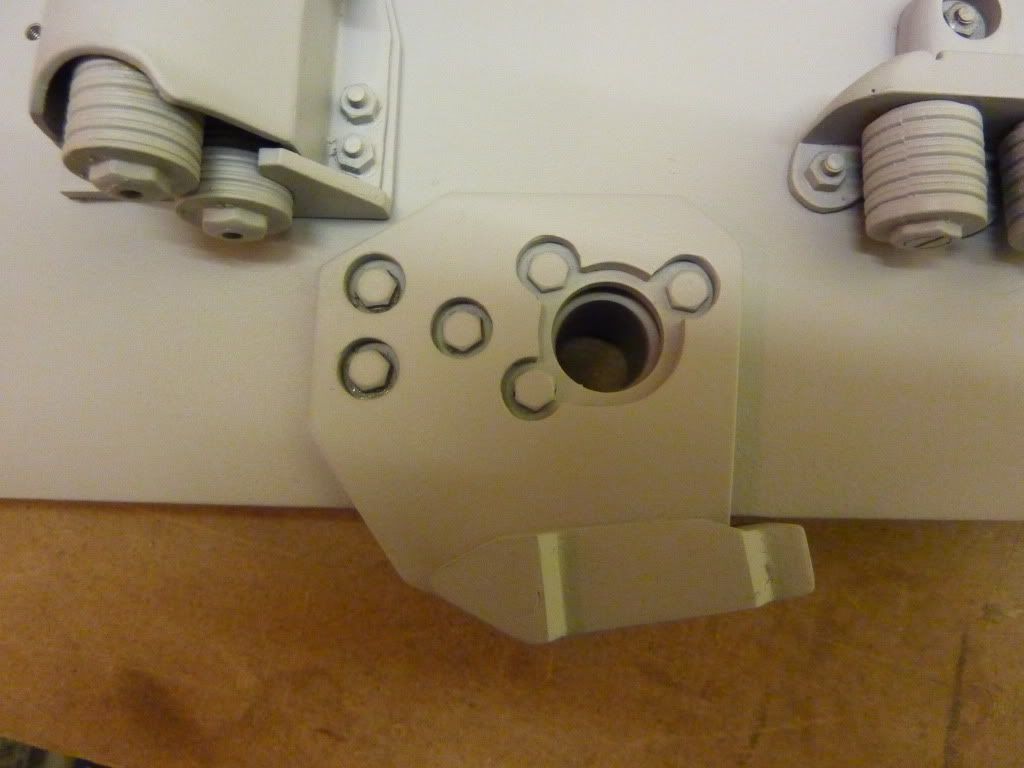
The final shot is for Kent showing the inside face of the Ansclagbock with the mount bolts retained by lock tabs
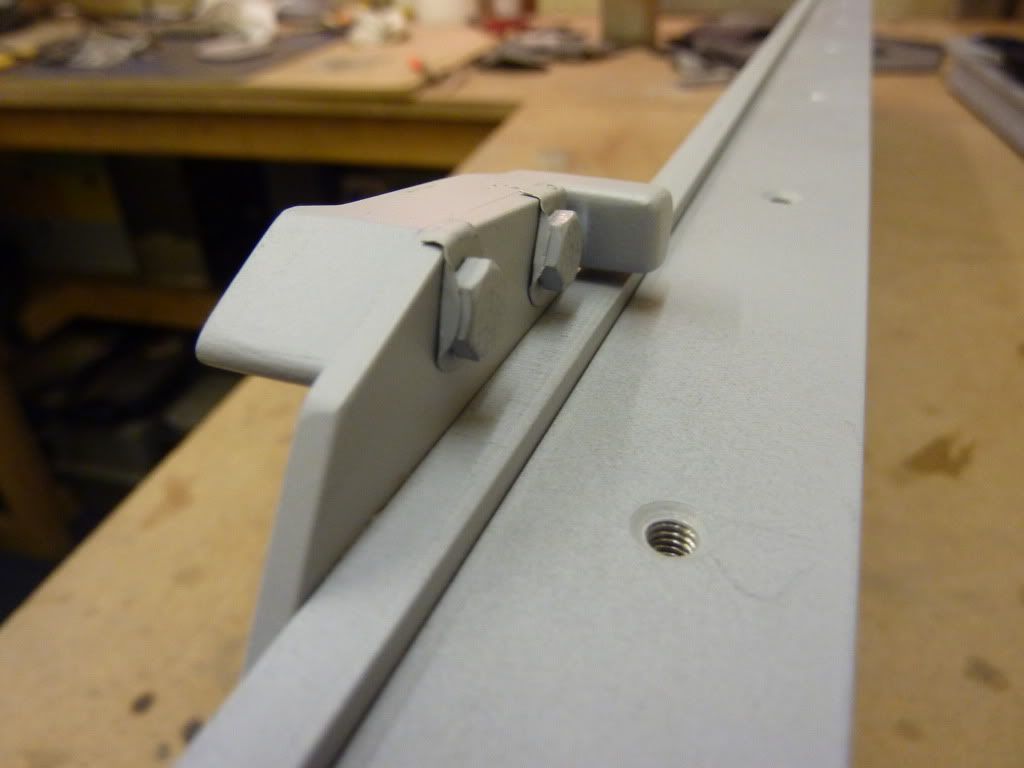
More to come
Steve
The first shot shows the dummy attachment bolts in position, 2 more bolts fit forward of these but because of the position of one of the torsion bar block attachment screws it was not possible to drill and tap at that position. Also shown are 3 predrilled and tapped holes for attaching the Anschlagbock plate.
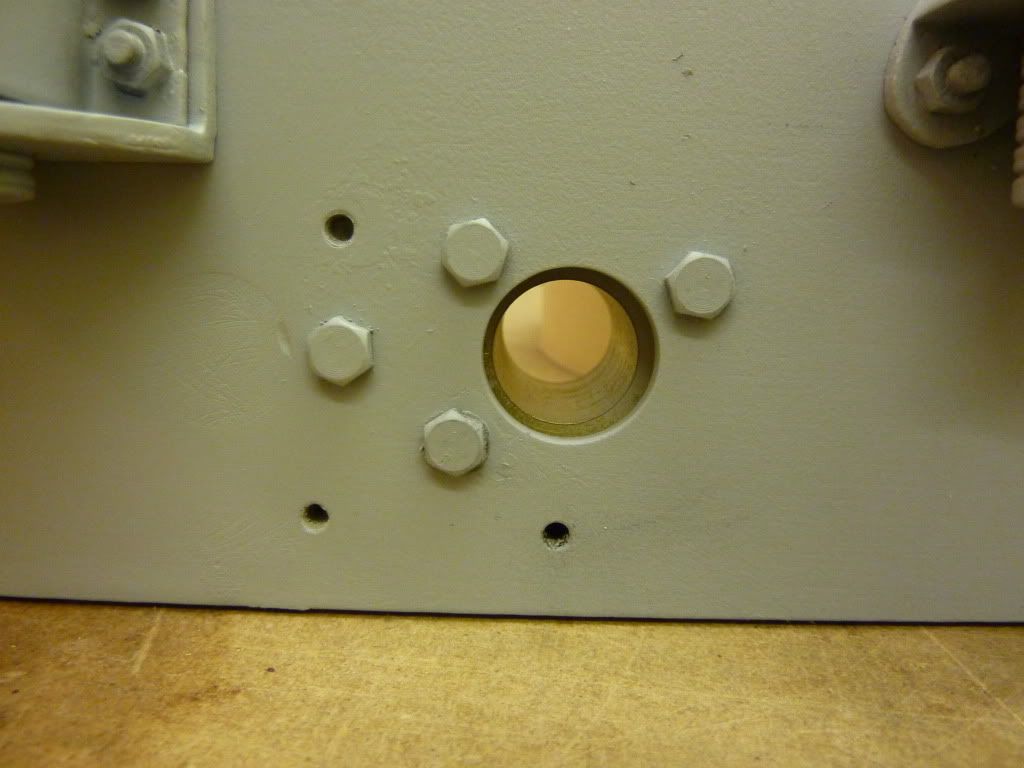
The next shot shows the Anschlagbock plate installed using 3 M3 csk bolts.
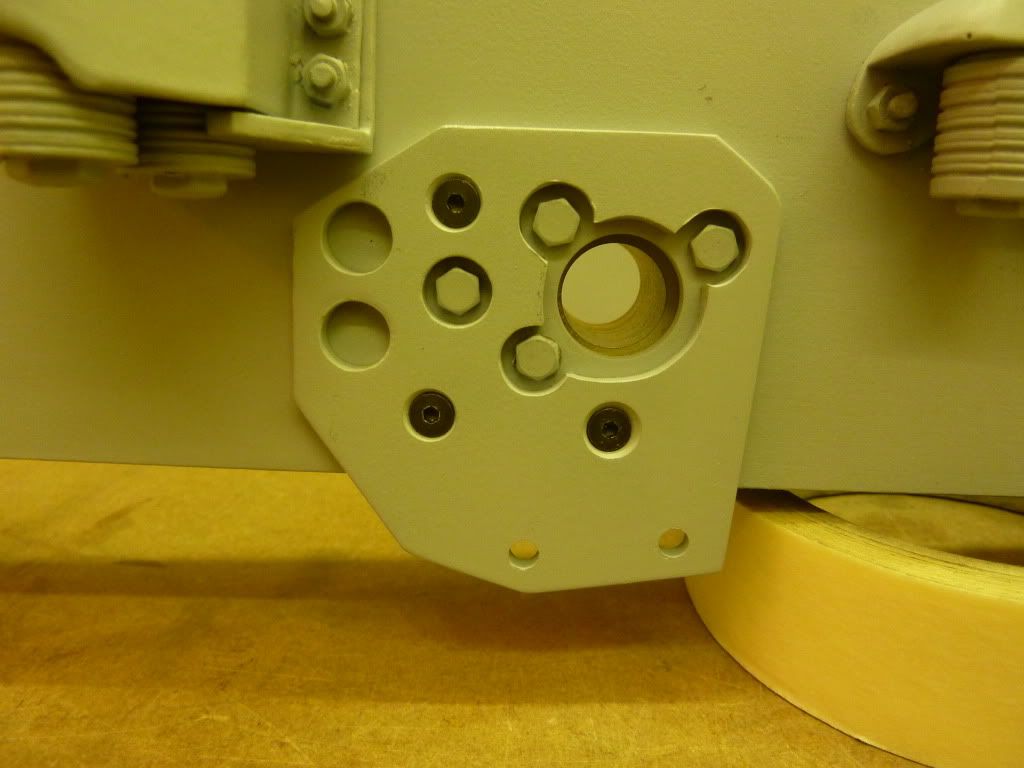
The next shot shows the final appearance of the Ansclagbock with the mounting screws filled and the 2 dummy bolts glued in place
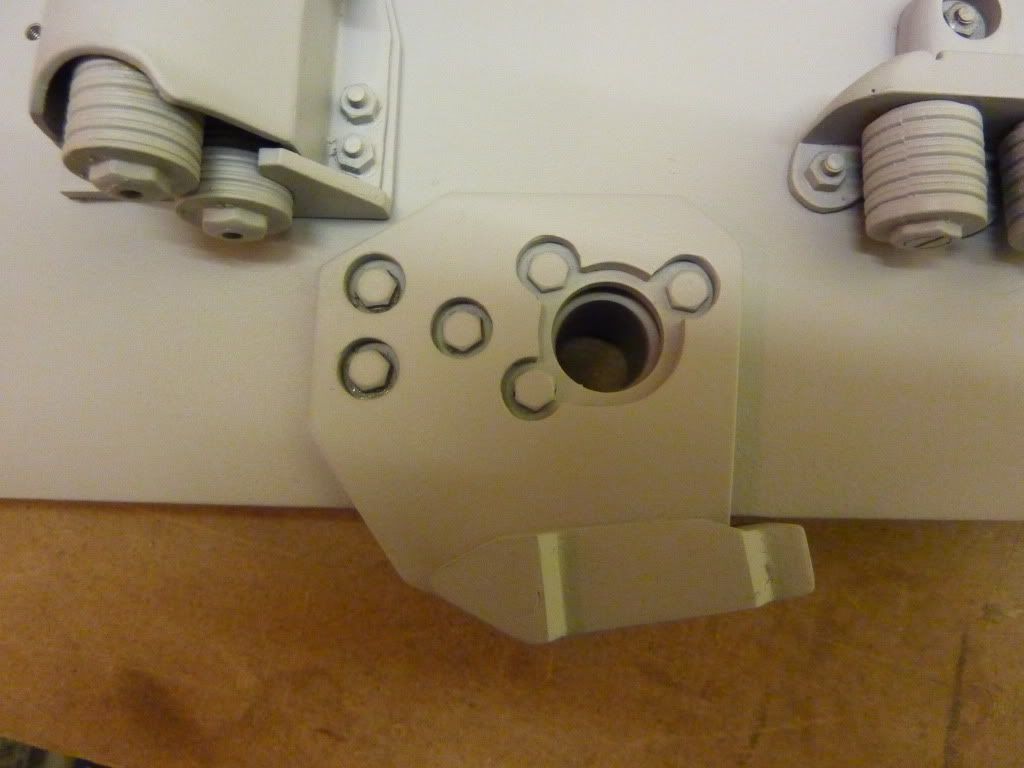
The final shot is for Kent showing the inside face of the Ansclagbock with the mount bolts retained by lock tabs
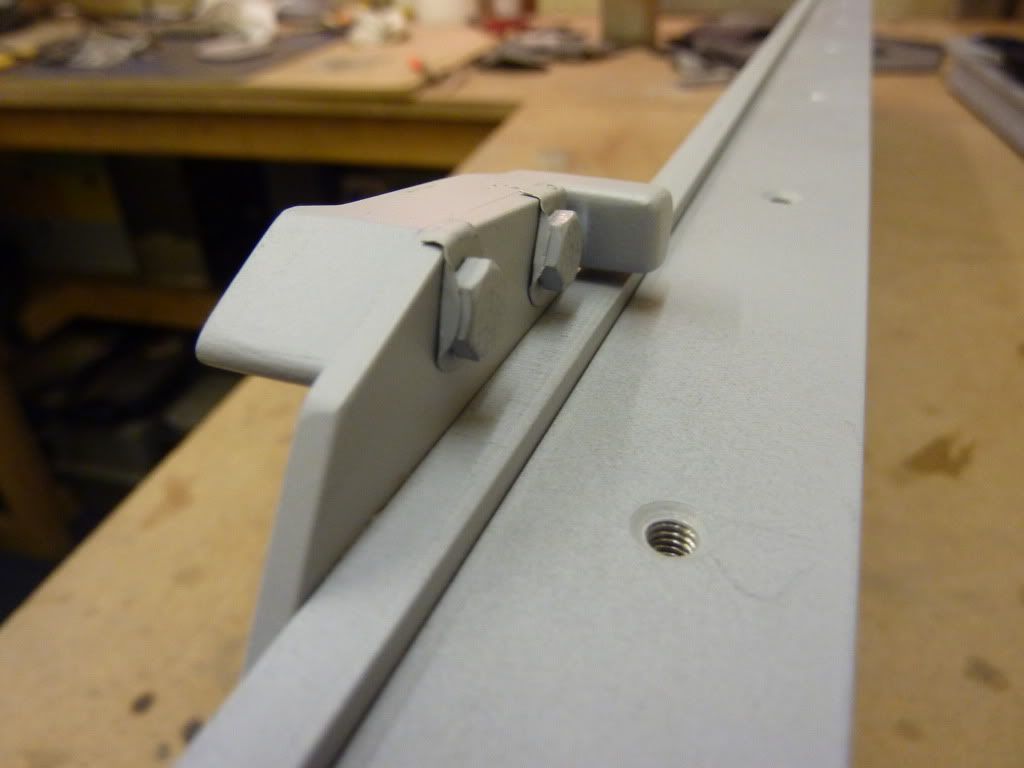
More to come
Steve
-
- Posts: 1228
- Joined: Thu Jul 12, 2007 11:42 am
- Location: Manchester
- Has liked: 8 times
- Been liked: 697 times
The next bits !
The hull sides have covers over internal suspension fittings so instead of cutting these individualy from sheet metal i decided to see if i could cast them.
This was the result.
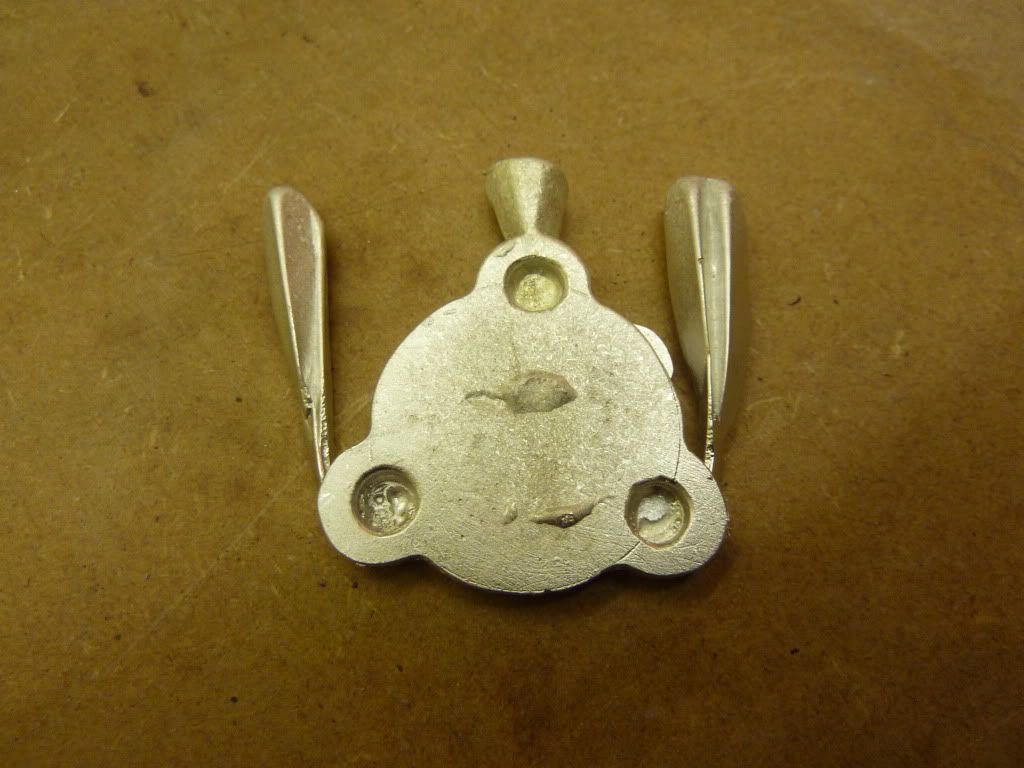
After an evenings casting i had the 16 i needed.
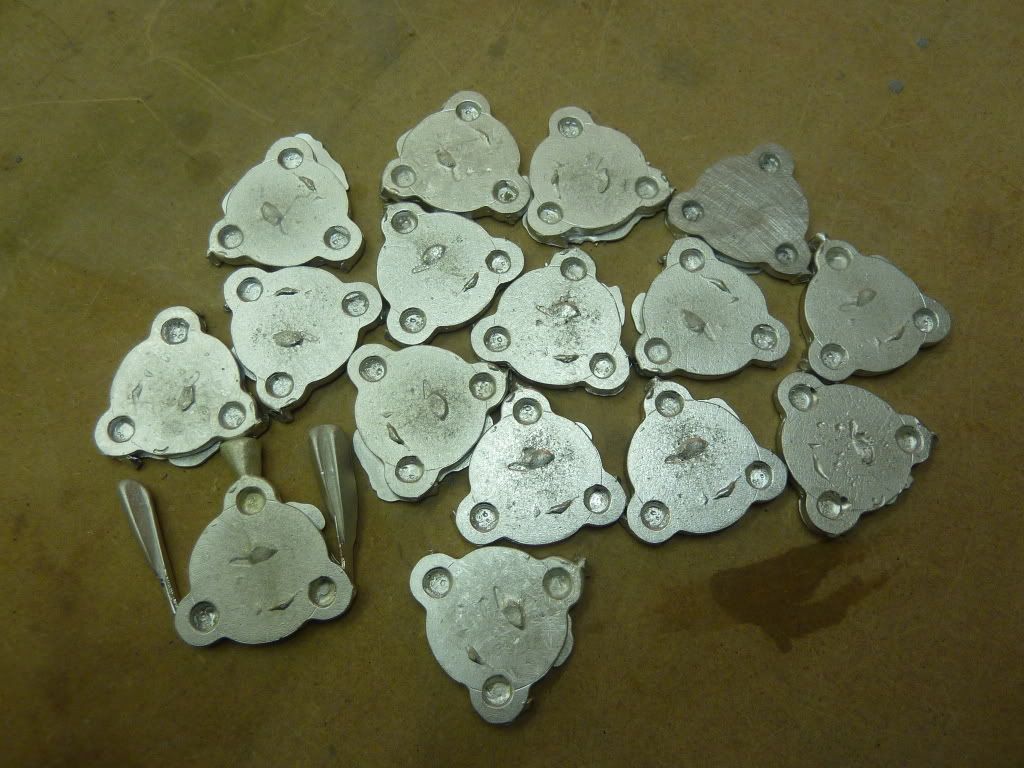
A bit of clean up and primer and almost ready to fit
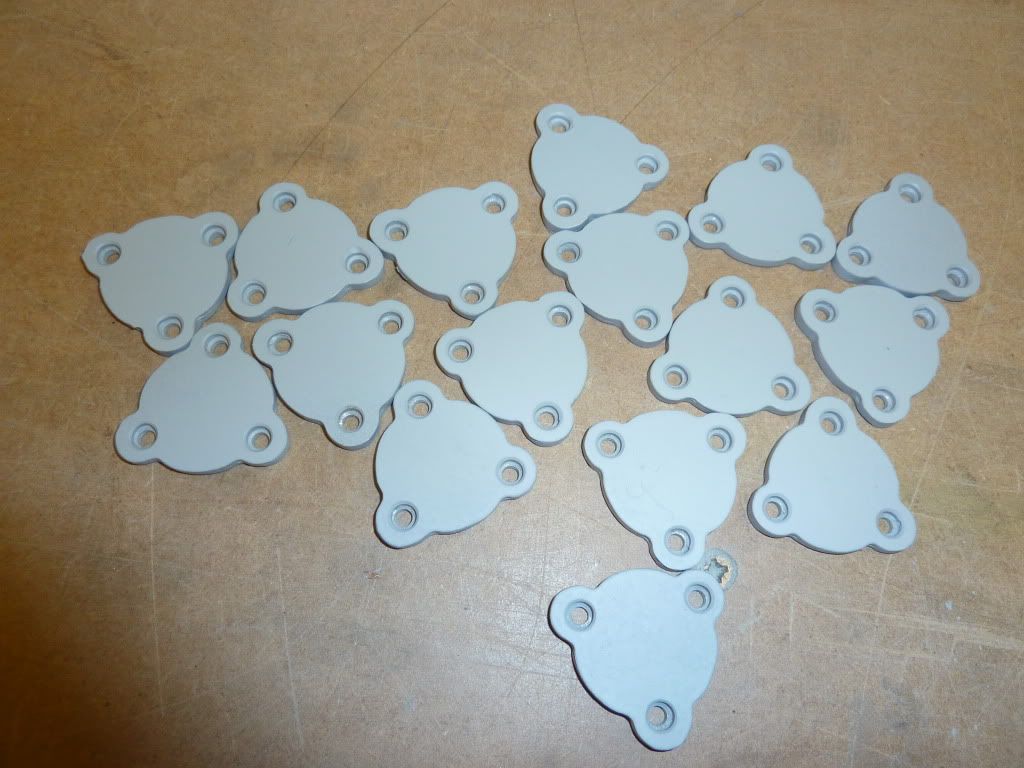
A bit of carefull marking out and drilling and the hull sides look like a seive.
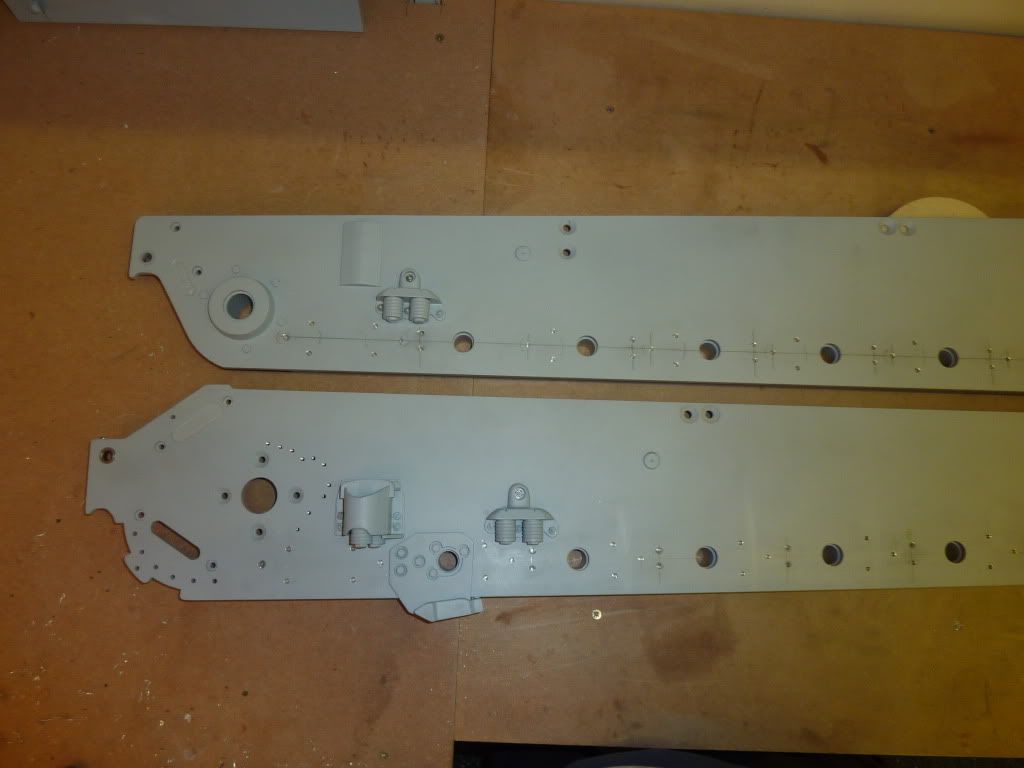
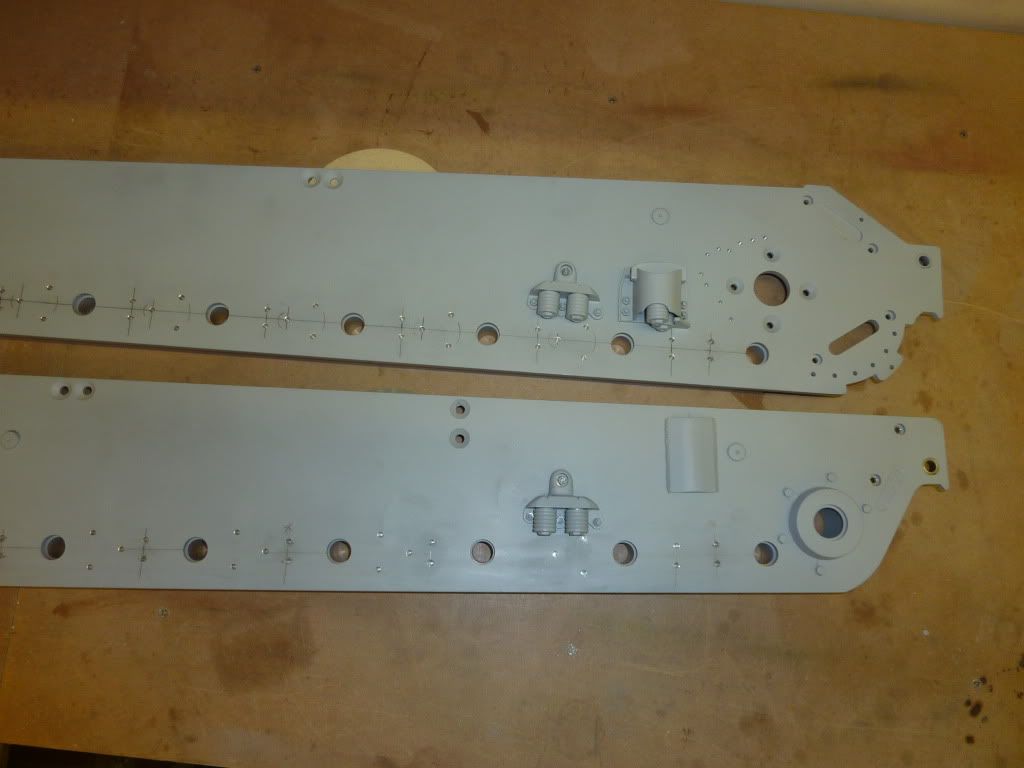
Covers fitted, looking a lot better.
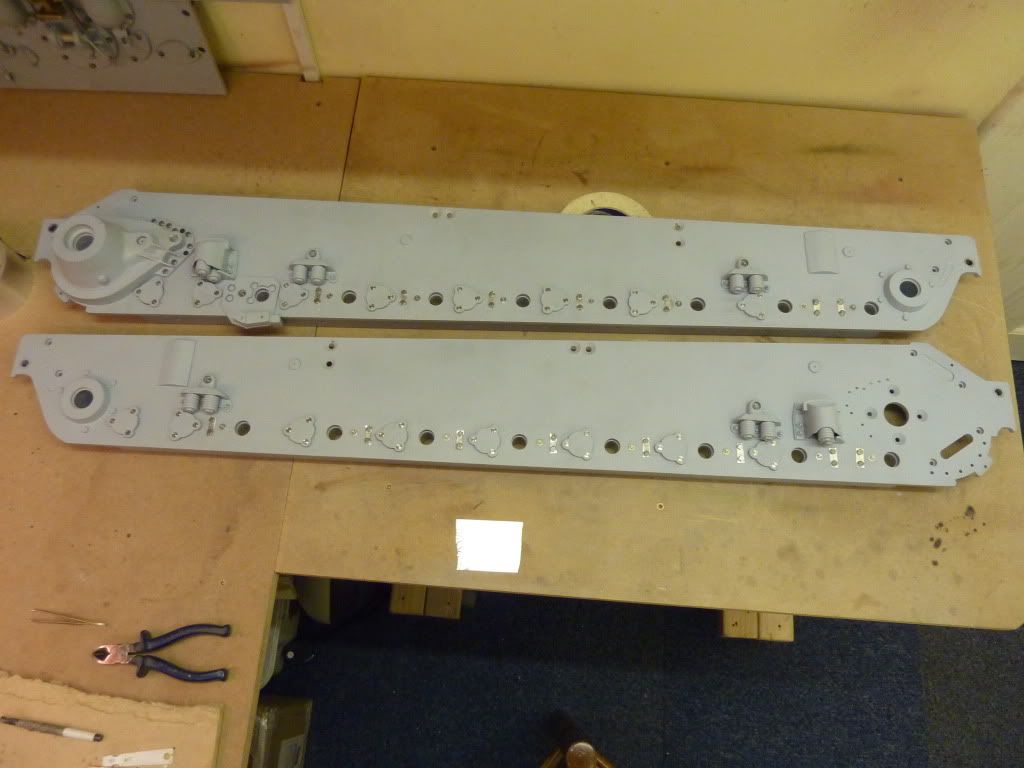
Finally a couple of closer shots showing the covers and additional bolts and fittings.
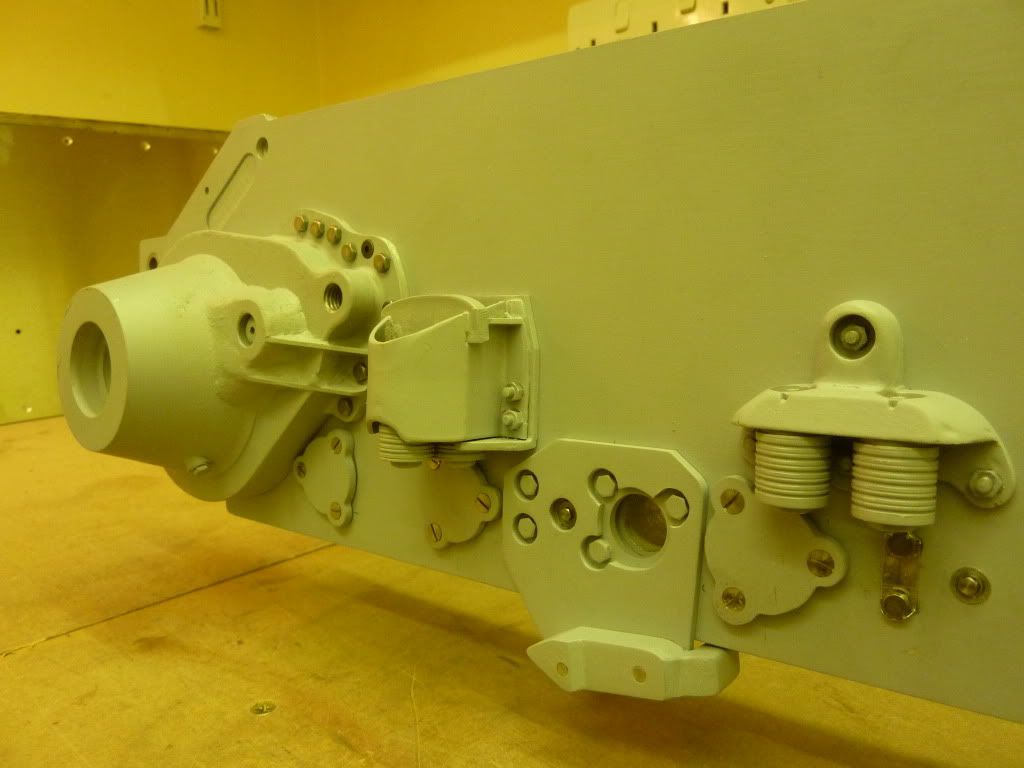
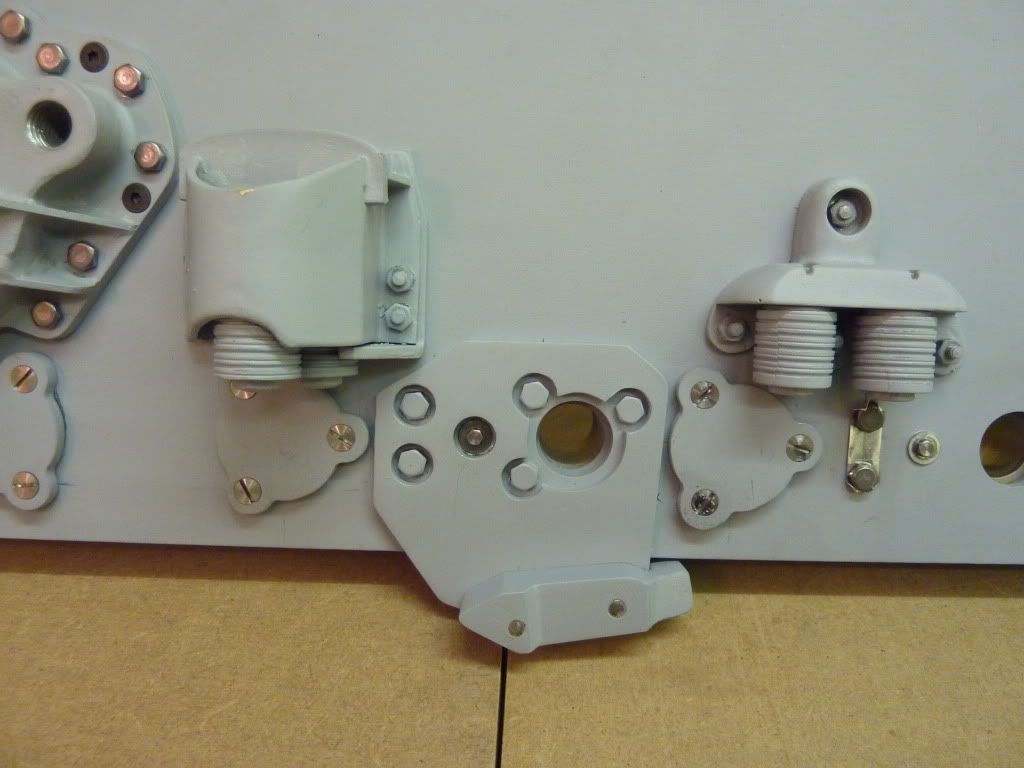
A very pleasing result but unfortunatly not a lot will be visable with the wheels on, But at least i know its there.
Regards
Steve
The hull sides have covers over internal suspension fittings so instead of cutting these individualy from sheet metal i decided to see if i could cast them.
This was the result.
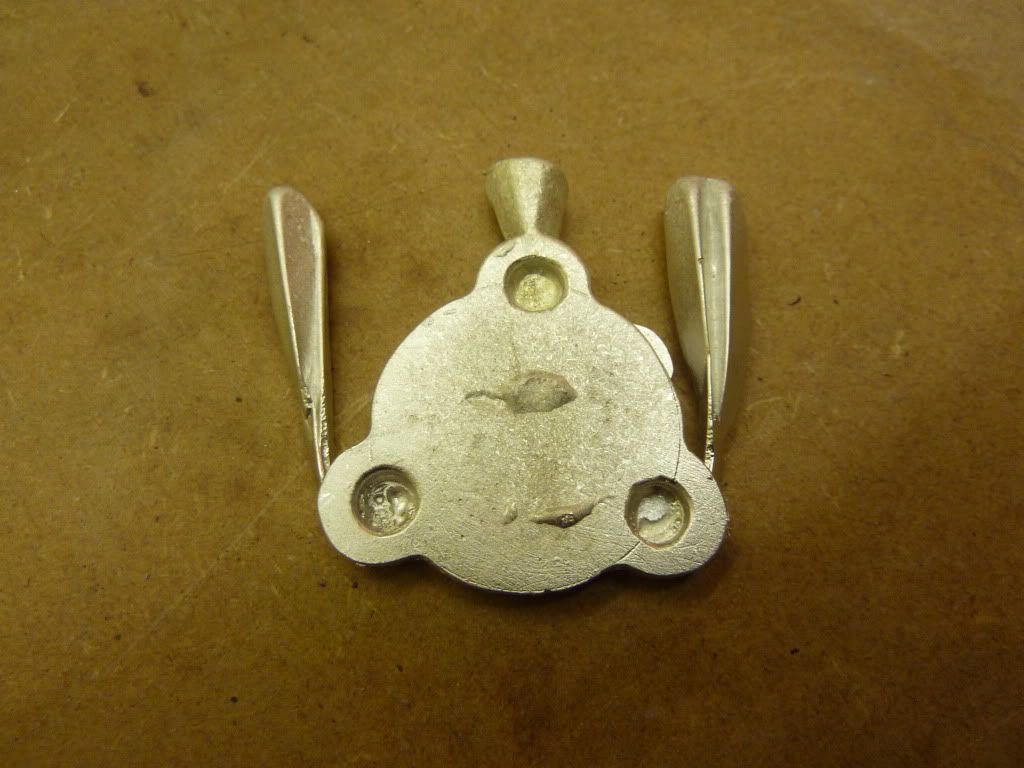
After an evenings casting i had the 16 i needed.
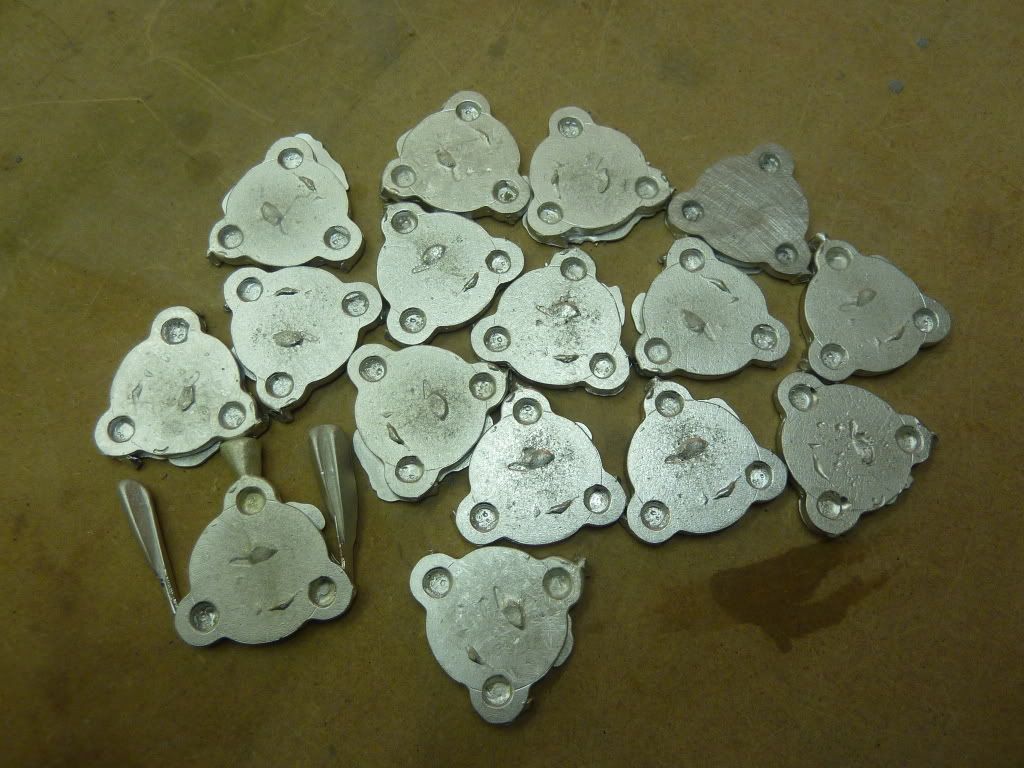
A bit of clean up and primer and almost ready to fit
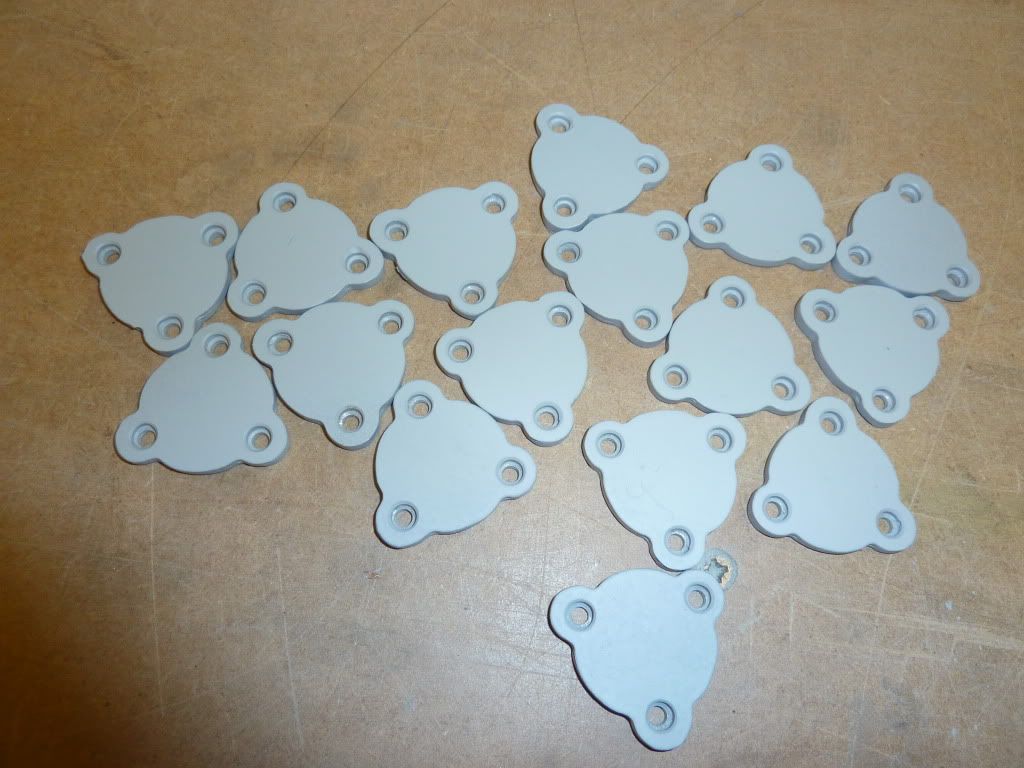
A bit of carefull marking out and drilling and the hull sides look like a seive.
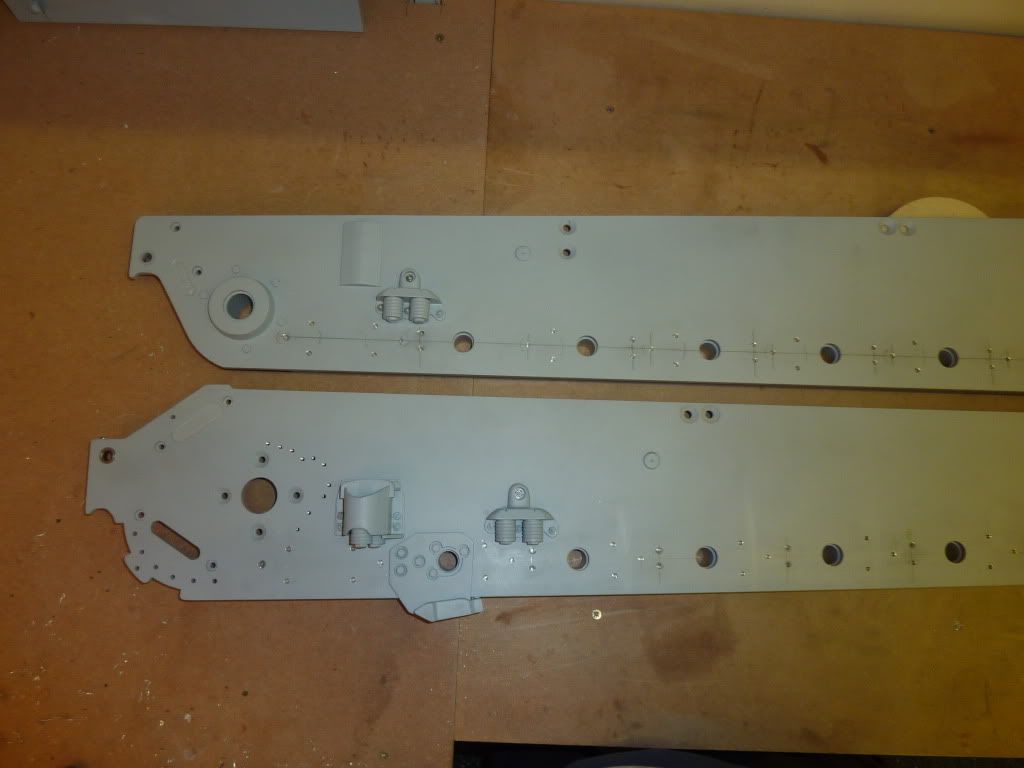
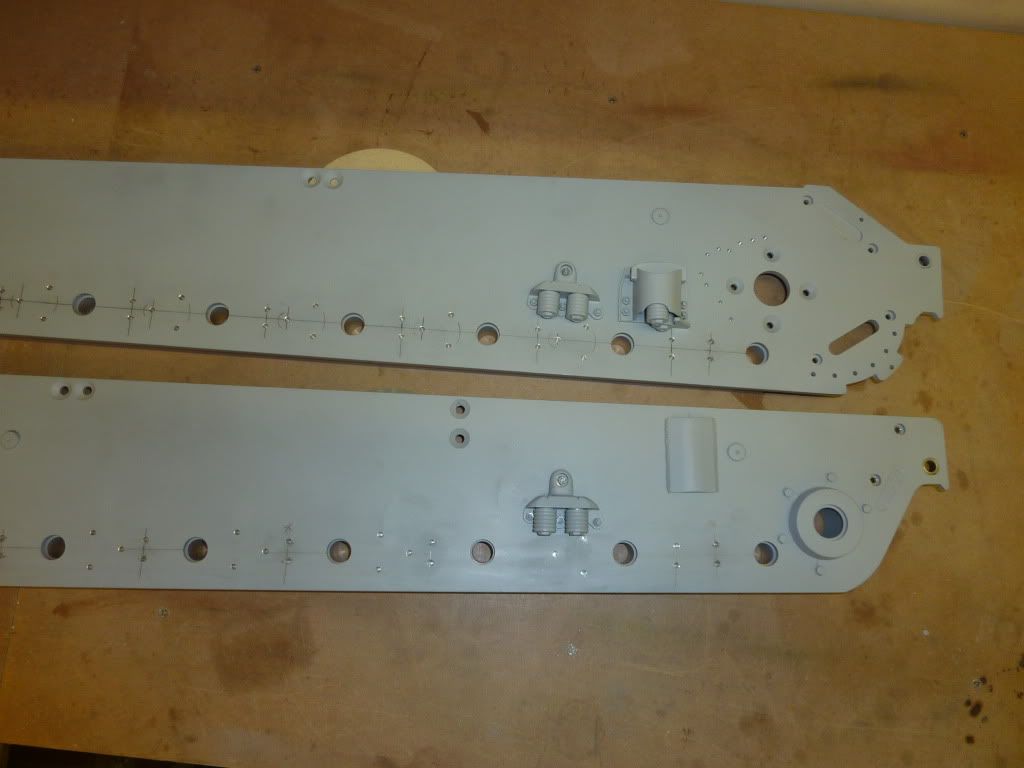
Covers fitted, looking a lot better.
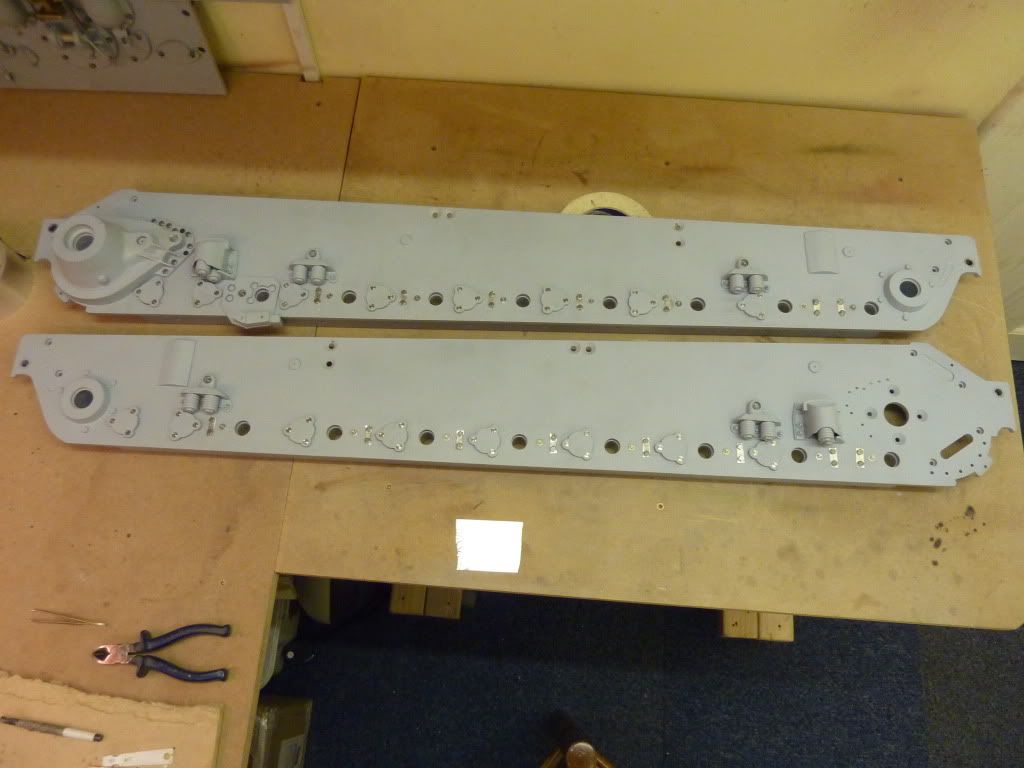
Finally a couple of closer shots showing the covers and additional bolts and fittings.
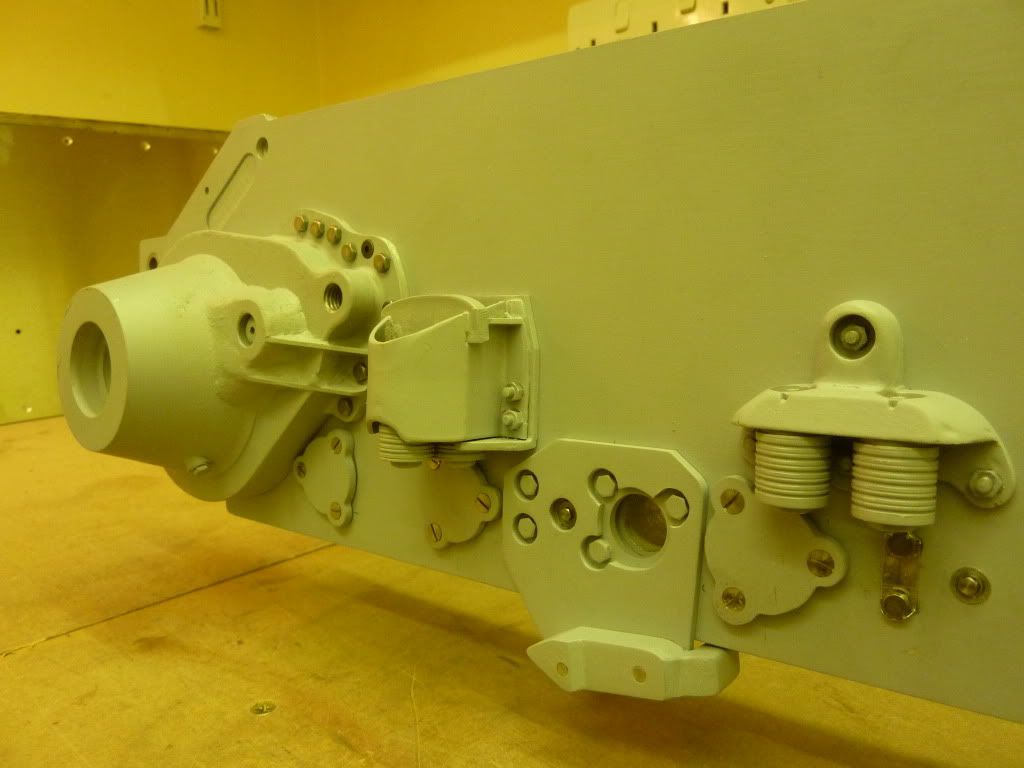
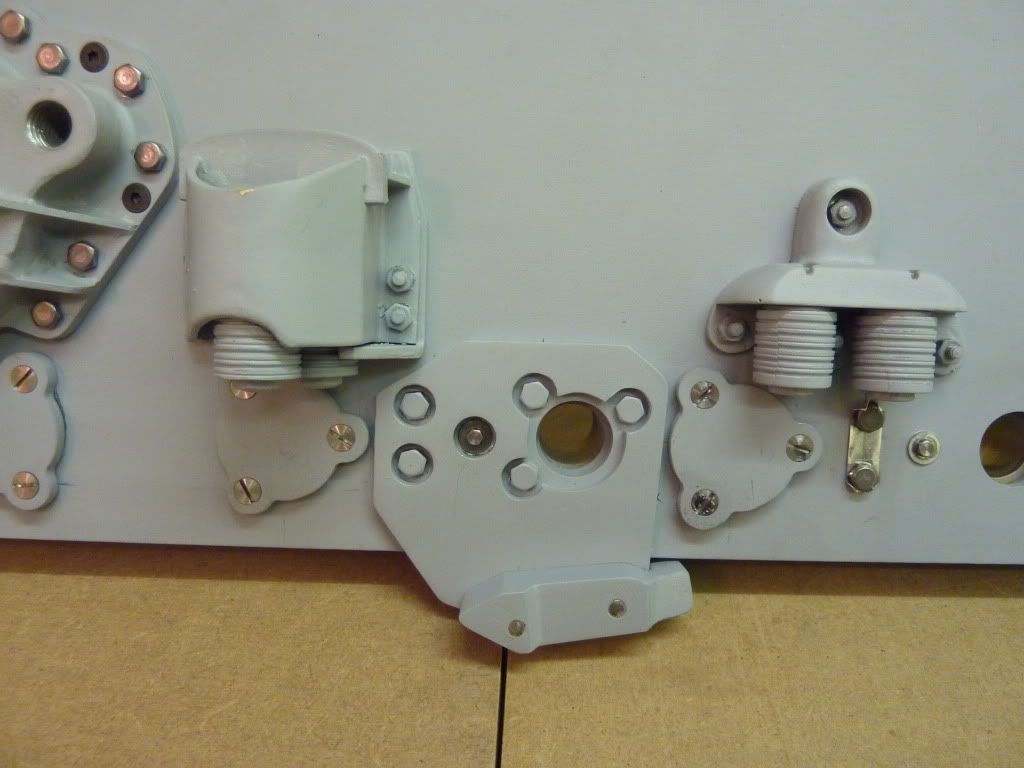
A very pleasing result but unfortunatly not a lot will be visable with the wheels on, But at least i know its there.
Regards
Steve
- Adrian Harris
- Posts: 5074
- Joined: Thu Jul 12, 2007 10:46 pm
- Location: Berkshire (UK)
- Has liked: 1420 times
- Been liked: 1595 times
Great looking parts Steve - were they dificult to cast ?
I'm surprised you appear to have done them vertically - but I suppose that stops you getting the dropped soufflé effect if they were flat ?
Adrian.
I'm surprised you appear to have done them vertically - but I suppose that stops you getting the dropped soufflé effect if they were flat ?
Adrian.
Contact me at sales@armortekaddict.uk for details of my smoker fan control module
-
- Posts: 2033
- Joined: Fri Nov 02, 2007 8:51 pm
- Location: new forest,hampshire,u.k.
- Been liked: 1644 times
-
- Posts: 363
- Joined: Tue Nov 18, 2008 4:15 pm
- Location: Auburn, Wa USA
- Been liked: 3 times
-
- Posts: 1559
- Joined: Thu Jul 12, 2007 4:44 pm
- Location: North Lancs
- Been liked: 68 times
Hi Steve.
Looking really good mate, you set the bar pretty high with your first Panther but this is going to beat it. Good stuff!
Cheers Paul
Looking really good mate, you set the bar pretty high with your first Panther but this is going to beat it. Good stuff!
Cheers Paul

Paul's Tank Workshop. Complete Tank builds and re builds zimmerit and paint to museum quality standard. pjtigerman@aol.com
01524 720977
https://www.facebook.com/PaulsTankWorkshop
01524 720977
https://www.facebook.com/PaulsTankWorkshop
-
- Posts: 289
- Joined: Tue Jul 24, 2007 7:22 pm
- Location: chesterfield derbyshire
- Been liked: 1 time
-
- Posts: 1228
- Joined: Thu Jul 12, 2007 11:42 am
- Location: Manchester
- Has liked: 8 times
- Been liked: 697 times
Hi Gents.
Thanks for all the positive comments.
Adrian, I spent quite a while thinking how best to produce the covers as i did not fancy cutting out 16 from sheet metal. Casting was the easiest way for me to produce these and after some thought i went for the method shown as i guessed it would produce parts with the least clean up to do. I was very pleased with results as they were all nice and flat with just the casting sprues and acouple of lumps and bumps to clean up.
Back to my next casting job
Steve
Thanks for all the positive comments.
Adrian, I spent quite a while thinking how best to produce the covers as i did not fancy cutting out 16 from sheet metal. Casting was the easiest way for me to produce these and after some thought i went for the method shown as i guessed it would produce parts with the least clean up to do. I was very pleased with results as they were all nice and flat with just the casting sprues and acouple of lumps and bumps to clean up.
Back to my next casting job
Steve
-
- Posts: 1825
- Joined: Tue Dec 14, 2010 3:11 pm
- Location: IRELAND,Dublin/Meath
- Has liked: 5 times
- Been liked: 672 times
- Contact: